摘要
折线配筋先张梁是一种新型的预应力混凝土梁,目前已在桥梁工程中开始应用。其较好的受力方式解决了直线先张梁跨度较小的不足,既保留了先张法的优点,又避免了后张法中诸多技术难题,能够有效地降低梁端的主拉应力,提高构件的耐久性和抗剪能力。折线配筋先张梁制作过程中,弯起器是关键构件之一,本文结合某环线工程,研究弯起器在钢绞线张拉中引起的预应力损失,进行了折线先张梁弯起器预应力损失试验,通过Workbench有限元软件对弯起器受力性能进行三维仿真参数化分析,为折线配筋先张梁弯起器的工程应用提供参考和数据支持。
Abstract
The pre-tensioned beam with folded-line reinforcement is a novel type of prestressed concrete beam and has been employed in bridge engineering currently. Its superior force-bearing pattern addresses the deficiency of the small span of the straight-line pre-tensioned beam. It not only retains the merits of the pre-tensioning method but also circumvents numerous technical predicaments in the post-tensioning method, effectively reducing the principal tensile stress at the beam end and enhancing the durability and shear resistance of the component. During the manufacturing process of the pre-tensioned beam with folded-line reinforcement, the bender is one of the key components. To explore the prestress loss induced by the bender during the tensioning of the steel strand, this paper, in combination with a certain ring road project, conducts a prestress loss test of the bender of the pre-tensioned beam with folded-line and undertakes a simulation study on the mechanical performance of the pulley-type bender via the Workbench finite element software, providing references and data support for the engineering application of the bender of the pre-tensioned beam with folded-line reinforcement.
Keywords
0 引言
近年来预应力技术广泛应用在工程领域中,目前中国在桥梁工程中采用后张法预应力梁居多(张春雷,2020)。后张法预应力梁体广泛应用后,其不足之处也逐渐体现出来,主要表现为锚固端压应力过大导致混凝土压碎、孔道压浆难以保证密实引起钢绞线锈蚀、梁体耐久性下降等(王新宇等,2010)。
先张法预应力梁具有制造周期短、节省材料、梁体耐久性好、便于工厂化预制等优点,还可以省去后张法中锚具、波纹管等(唐芳,2017),避免后张法中可能出现的波纹管中压浆不密实、堵孔,影响结构耐久性等问题(李洞明,2019)。其中直线型配筋的先张法预应力梁体最为常见,整体梁体制作和使用过程预应力损失较小(刘立新,2010)。但因结构受力所限,直线型配筋的先张法梁体限于跨度在 20 m以下的中小跨径桥梁(杨毅和郑俞,2022)。折线形先张法预应力混凝土结构突破了直线先张法仅限于中小跨度的限制,同时施工相对简单,施工质量便于控制,采用预应力筋弯折施工技术,降低梁端主拉应力,改善梁体受力状况,实现对外荷载的有效平衡,是一种可靠合理的传力结构形式(秦晓勇,2017),配合台座的使用更适合量产(王艳等, 2013)。与直线型配筋的先张法预应力梁相比,折线配筋先张法预应力梁耐久性更好,截面受力形式更合理(张子璐等,2017),青藏铁路 24 m 折线先张梁(柳学发和陈良江,2004)、桐柏淮河公路桥 35 m 折线先张箱梁(王俊等,2009)、山东黄河大桥 50 m 折线配筋先张T梁(王亚辉,2007)等均已成功实践。与直线先张梁相比,实现折线预应力是在台座上的关键构件弯起器,预应力筋通过弯起器后会产生一定的预应力损失(徐小珊,2016)。目前,科研人员对折线先张梁关键部位的局部应力分布特点进行了较为深入的研究(黄文雄和谭利英,2012),而弯起器所致的预应力损失及其仿真分析,目前还属于研究空白阶段。
1 钢绞线分级张拉试验
预应力筋的弯折、导向、定位和成形,需借助固定于台座上布置的弯起器来实现(王辉等,2007),弯起器是折线配筋先张法结构得以实现的关键构件(Wang et al.,2013)。预应力由张拉端传递至锚固端,经过弯起器产生摩擦阻力,导致预应力损失。本文采用分级张拉钢绞线的方法,测试弯起器所致预应力损失的数值(黄文雄和谭利英,2013b)。
1.1 试验设计
张拉台座各构件分部图如图1所示,其构造及加工过程为:首先将现浇混凝土倒入模具,完成底座与反力墙混凝土浇筑并预留孔道,养护达到设计强度后,依次安装钢结构张拉台座、b弯起器、a弯起器,然后通过高强度锚固螺栓将其与混凝土底座连为整体。a、b 弯起器,均采用同类型的弯起器。张拉台座安装完成后,穿入钢绞线,通过改变钢绞线位于 b 弯起器的放置位置来设置转向角度,可调整的角度分别为1°、3°、5°、7°、9°、11°,共6个角度。同时,压力传感器分别安装在张拉端和锚固端,监测预应力筋轴力情况。准备完毕后,通过穿心千斤顶对钢绞线进行分级张拉。弯起器受力示意图见图2。
为减小材料强度不足对试验结果的影响,本试验钢绞线采用高强度低松弛预应力钢绞线 Φs15.2 mm(270 级),采用 Q345 级钢材制作芯轴和弯起器 (图3)。弯起器凹槽部位功能是定位和导向,以及弯折钢绞线、调整转向角度。
在钢束各截面布置应变片的方法被广泛用来监测钢束应力和损失情况,特别在现场试验中操作更为方便(黄文雄和谭利英,2013a)。然而由于钢绞线钢丝较细且多根绞合在一起,使得应变片的实际布置位置容易出现偏差,从而使测试结果出现偏差;而应变片主要沿钢束钢丝轴向布置,与钢束轴线成一较小角度,也可使测得的钢绞线应力出现一定偏差。为减小测试结果偏差,通过多次重复的测量,求平均值来减小随机偏差的影响(黄文雄,2012)。
图1试验台座
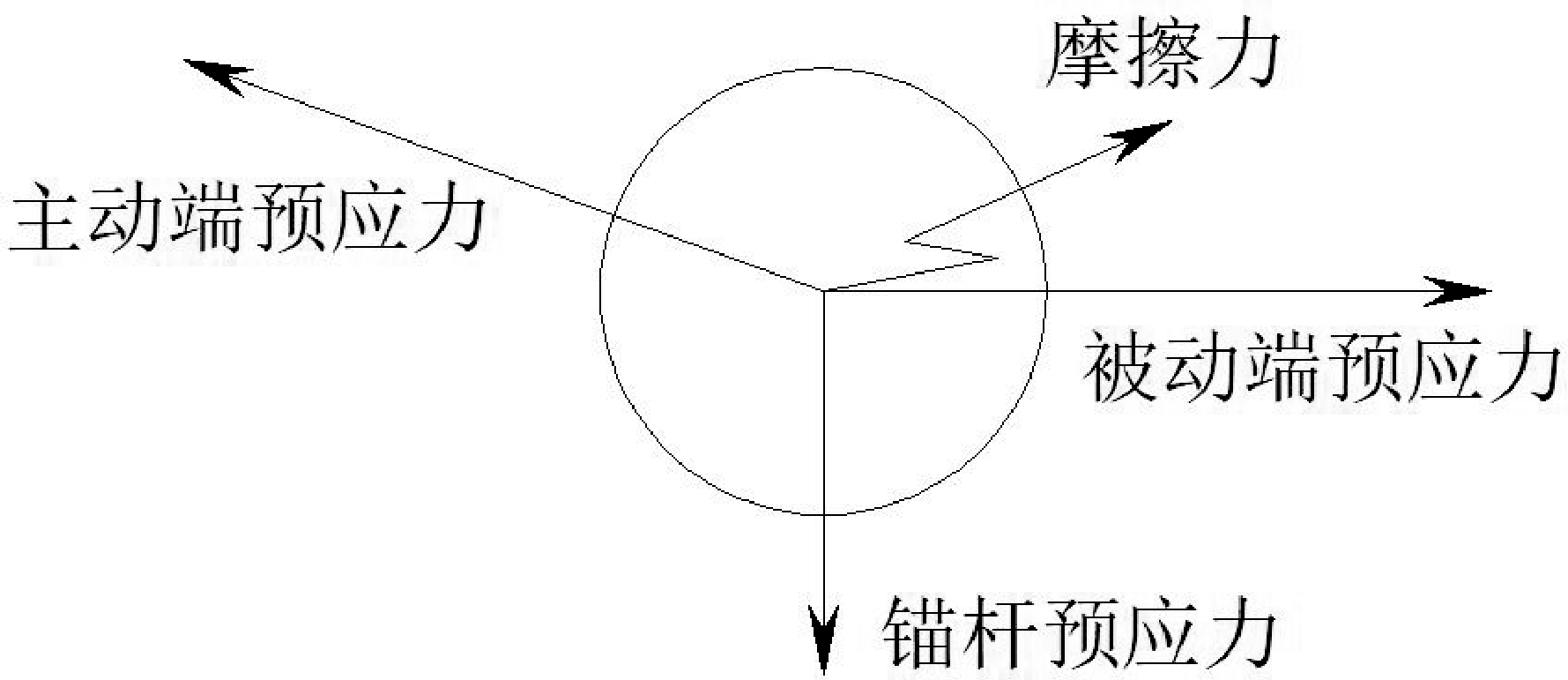
图2弯起器受力示意图

图3弯起器实物图
1.2 水平(0°)张拉试验
通过水平(0°)张拉试验,消除张拉端预应力损失的影响。通过张拉端与锚固端压力传感器数值所计算得到的差值来确定张拉端和锚固端预应力损失值,经过多次测试计算,得出不同荷载等级下损失值(表1)。在处理其他 6种转向角度的结果时扣除水平张拉工况下张拉端和锚固端引起的总损失后便可得到弯起器所致预应力损失。
表1不同荷载等级下水平(0°)张拉预应力损失值

1.3 不同角度张拉试验
通过张拉端与锚固端压应力差值,计算钢绞线通过两种弯起器的预应力损失情况。考虑 1°、3°、 5°、7°、9°、11°,共6种转向角度,张拉应力为0.72fpk= 1339.2 MPa,分 9 级进行张拉和测试每级张拉不超过控制张拉力的10%,每级持荷5 min。
在各荷载等级下,扣除水平(0°)张拉预应力损失值后,1°、3°、5°、7°、9°、11°角度下a、b弯起器所致预应力损失值(图4)。可见,随着荷载等级的增大,转向角度越大,预应力损失值增长越快;在相同荷载等级下,转向角度越大,预应力损失值越大。单个弯起器损失率(表2),转向角度越大,预应力损失率越高。
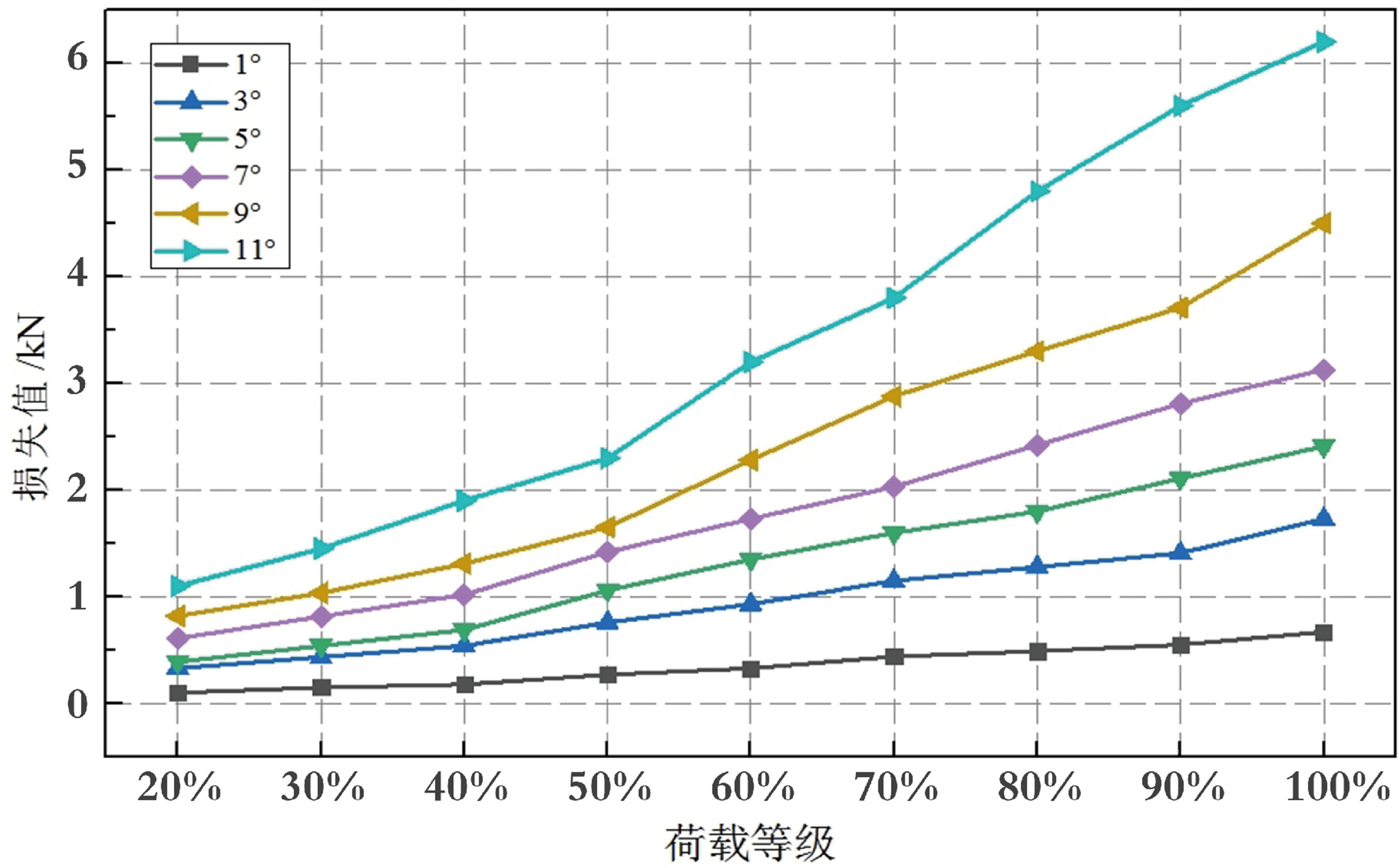
图4不同转向角度下弯起器损失值
表21°、3°、5°、7°、9°、11°角度下单个弯起器损失率

2 仿真计算
本文拟采用通用有限元软件 Workbench,从受力变形后弯起器的整体最大位移和最大应力2个方面对弯起器的力学性能进行整体受力分析,采用三维实体单元建立有限元模型,根据实际模型尺寸,进一步为实际应用提供理论分析依据(王琰和侯国清,2024)。由于张拉台座分布有 a、b 两个弯起器,所受张拉力在这两个弯起器上进行了平均分配,因此可以只取其中一个弯起器进行模型分析。
2.1 几何模型
弯起器的三维几何参数化模型采用Mechanical APDL命令流建立(赵艳梅,2018),几何模型由弯起器滑轮、弯起器芯轴和钢绞线组成(图5),Z轴反方向为张拉端,正方向为锚固端。角度初始设定为10°。
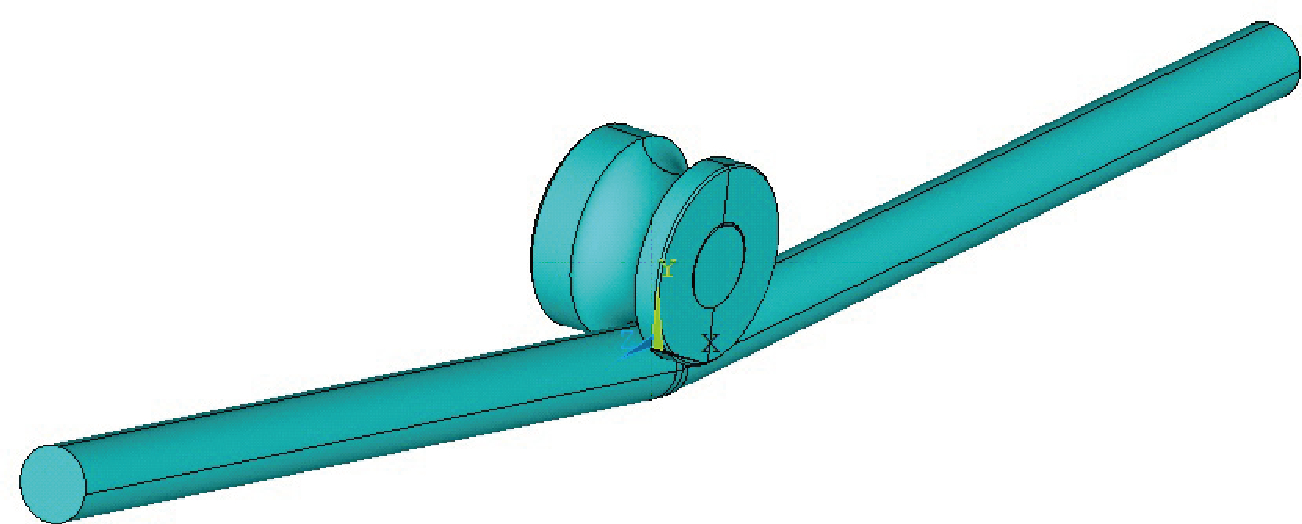
图5几何模型
张拉力通过张拉端传递到锚固端,途经弯起器产生摩擦损失,因此在几何模型中于钢绞线与弯起器滑轮、弯起器滑轮与弯起器芯轴接触部位设置两个接触对,在计算时将张拉力作用于张拉端,模拟试验受力情况,将芯轴两端与锚固端固定。
2.2 有限元模型的建立
将 Mechanical APDL 中建立好的几何模型,导入 Workbench 有限元软件中,通过对弯起器各个构件赋予材料属性、截面类型、单元类型、定义接触、划分单元以及施加荷载等,将几何模型转化为有限元模型。
(1)材料定义:预应力筋采用 Φs15.2 mm(270 级)高强度低松弛预应力钢绞线,弯起器滑轮和芯轴均采用Q345钢,在Workbench软件自带的各类材料中,选择对应的材料属性进行定义,主要涉及到的材料参数为材料的密度、弹性模量、泊松比、屈服强度以及切线模量。
(2)接触设置:需设置的位置为钢绞线与弯起器滑轮接触处、滑轮与芯轴接触处,钢绞线与滑轮接触时将钢绞线接触面定义为主面,滑轮接触面定义为从面,滑轮与芯轴接触时将滑轮接触面定义为主面,芯轴接触面定义为从面(图6)。接触类型设置为Frictional,摩擦系数设置为0.15。

图6各部件接触定义
a—钢绞线与弯起器接触定义;b—弯起器与芯轴接触定义
(3)网格划分:网格尺寸取为1.5 mm,接触部位适当加密,网格尺寸取1 mm,划分网格后的模型(图7),整个模型实体单元数为34717个。

图7网格划分
(4)施加荷载:根据实验室试验 100% 荷载工况下,张拉荷载设置为 180 kN,荷载施加方式是对钢绞线张拉端几何中心施加垂直于面的集中力,芯轴端面与锚固面设置为Fixed Support。
2.3 数值模拟结果分析
Workbench软件作为一款常用的具有强大功能的有限元分析软件,兼具有静力分析的功能(田苗和王家林,2009),本文中弯起器的受力计算属于静力问题。通过改变钢绞线的弯折角度来计算不同角度下弯起器所致预应力损失。
(1)变形分析:通过计算分析得出,在 100% 荷载工况下 10°转向角度构件位移如图8a所示,位移最大值出现在钢绞线的张拉端附近处为1.848 mm。滑轮与轴承位移最大值出现在接触面附近,分别为 0.95894 mm与0.20704 mm。
(2)应力分析:通过计算分析得出,在 100% 荷载工况 10°下转向角度下应力分布,应力最大值出现在钢绞线与滑轮接触处,为 1579.3 MPa,具体应力分布如图8b所示。滑轮与轴承位移最大值出现在接触面附近,分别为 260.77 MPa 与 332.19 MPa,具体应力分布如图8c、8d所示。
(3)接触分析:两对接触面接触情况如图12 所示,压力最大值出现在接触位置,为574.88 MPa(图8e),摩擦应力最大值为 83.144 MPa(图8f),均出现在钢绞线与滑轮接触点附近,滑行最大距离出现在芯轴与滑轮接触部位,数值为0.41024 mm(图8g)。
图8数值模拟结果
a—位移变形图;b—钢绞线应力分布;c—滑轮应力分布;d—芯轴应力分布;e—压力分布图;f—摩擦应力图;g—滑动距离图
表3弯起器损失率仿真结果

(4)预应力损失:10°转向角下,锚固端计算得出数值为 176.25 kN,单个弯起器所致预应力损失为 3.75 kN。通过对几何模型转向角度参数化,运用以上分析计算方法依次对 1°、2°、3°、4°、5°、6°、7°、8°、 9°、11°、12°、13°转向角度下弯起器所致预应力损失进行了计算分析,结果见表3。
试验与仿真计算单个弯起器预应力损失率对比结果如图9所示,有限元软件计算与试验所得的损失率趋势一致,结果吻合较好,说明有限元模型建立合理。
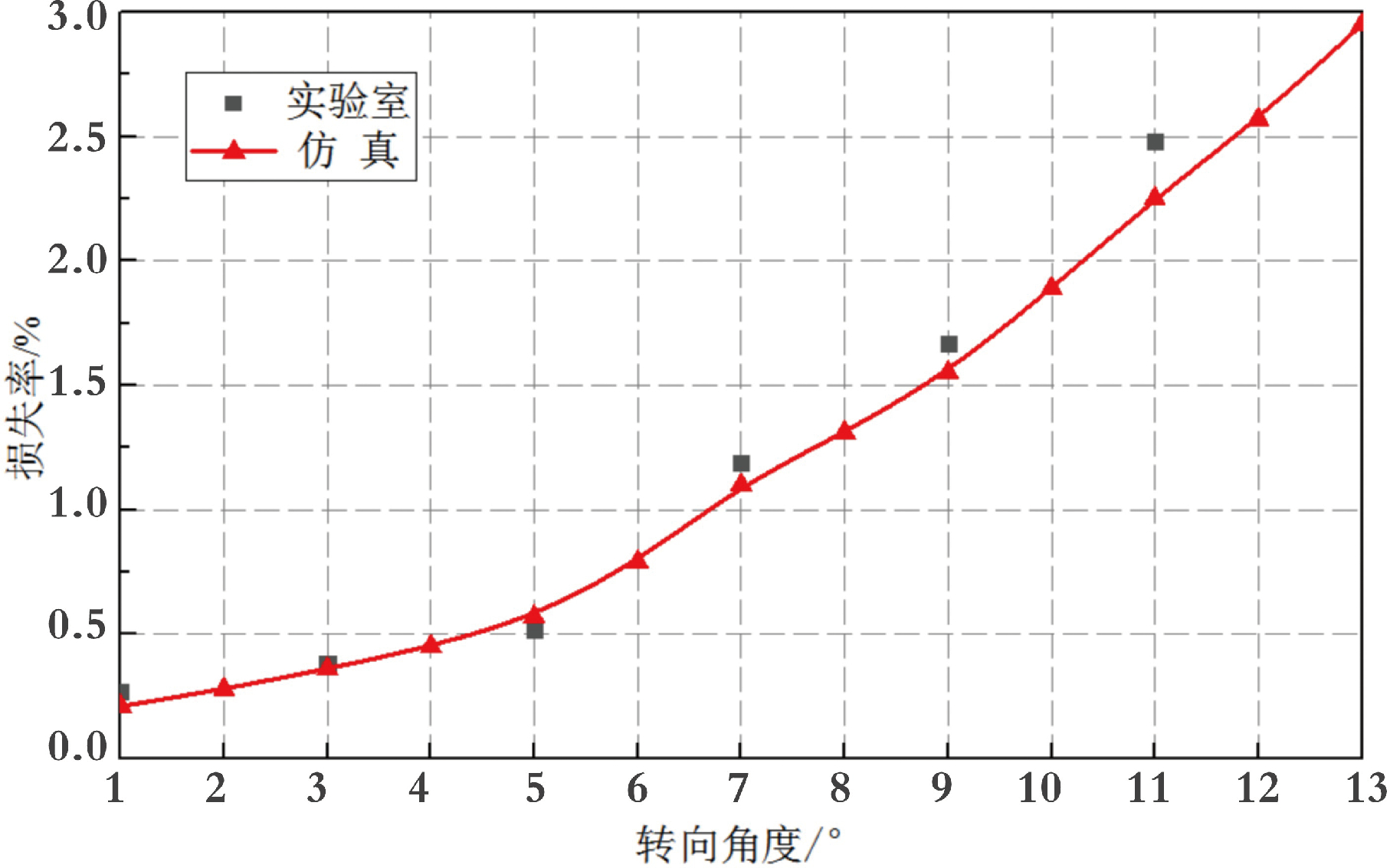
图9实测与仿真数据对比
3 结语
本文通过折线先张梁弯起器预应力损失试验和弯起器受力性能三维仿真参数化分析,研究了弯起器在钢绞线张拉中引起的预应力损失,主要结论如下:
(1)该试验中预应力张拉台座各部件设置合理,整体可靠。预应力筋通过弯起器后会产生预应力损失,通过收集应变片数据,计算 1°、3°、5°、7°、 9°、11°,6 种转向角度在各荷载等级下的预应力损失,并通过水平(0°)张拉试验,消除张拉端预应力损失的影响。当设置弯起角度为 1°时,预应力损失最低,设置弯起角度为 11°预应力损失最大,预应力损失值随弯起角度增大、荷载等级增加均呈正向相关。
(2)使用 Mechanical APDL 中建立弯起器几何参数化模型,并导入Workbench有限元软件中,建立弯起器三维实体单元有限元参数化模型,通过有限元软件 Workbench 进行整体受力分析,能够较好地反映接触对的接触情况以及应力分布,损失率曲线与试验结果整体吻合较好,说明该模型的正确性,可用于参数分析研究。
(3)1°、3°、5°转向角度下,预应力损失仿真结果与试验结果数据基本一致,7°、9°、11°转向角度下,预应力损失仿真结果与试验结果数据有部分偏差,随转向角度增大,偏差也随之增大。由此分析,在仿真模型建立中需进一步考虑预应力松弛、锚固段和张拉端钢绞线长度等因素对预应力损失的影响,此外不同转向角度弯起器与钢绞线摩擦系数的变化,可以作进一步分析。

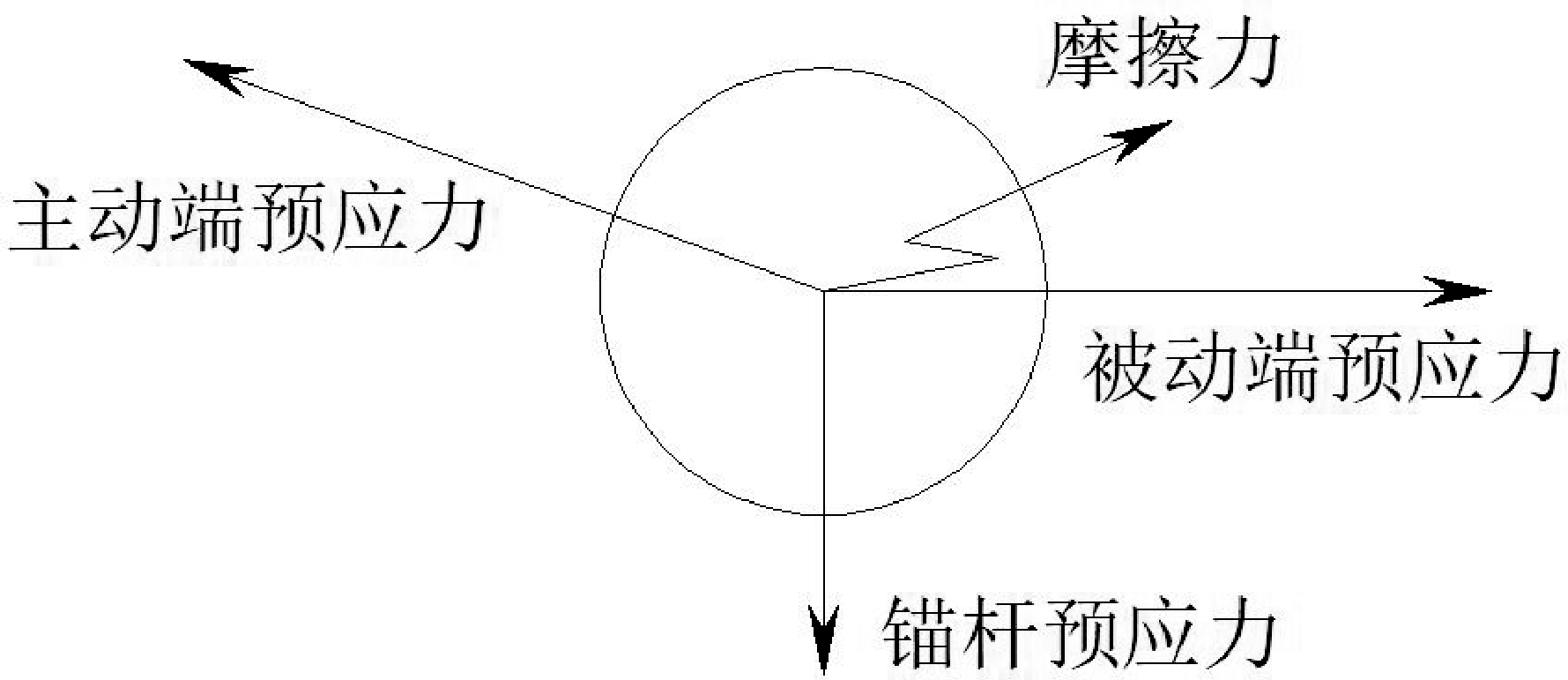

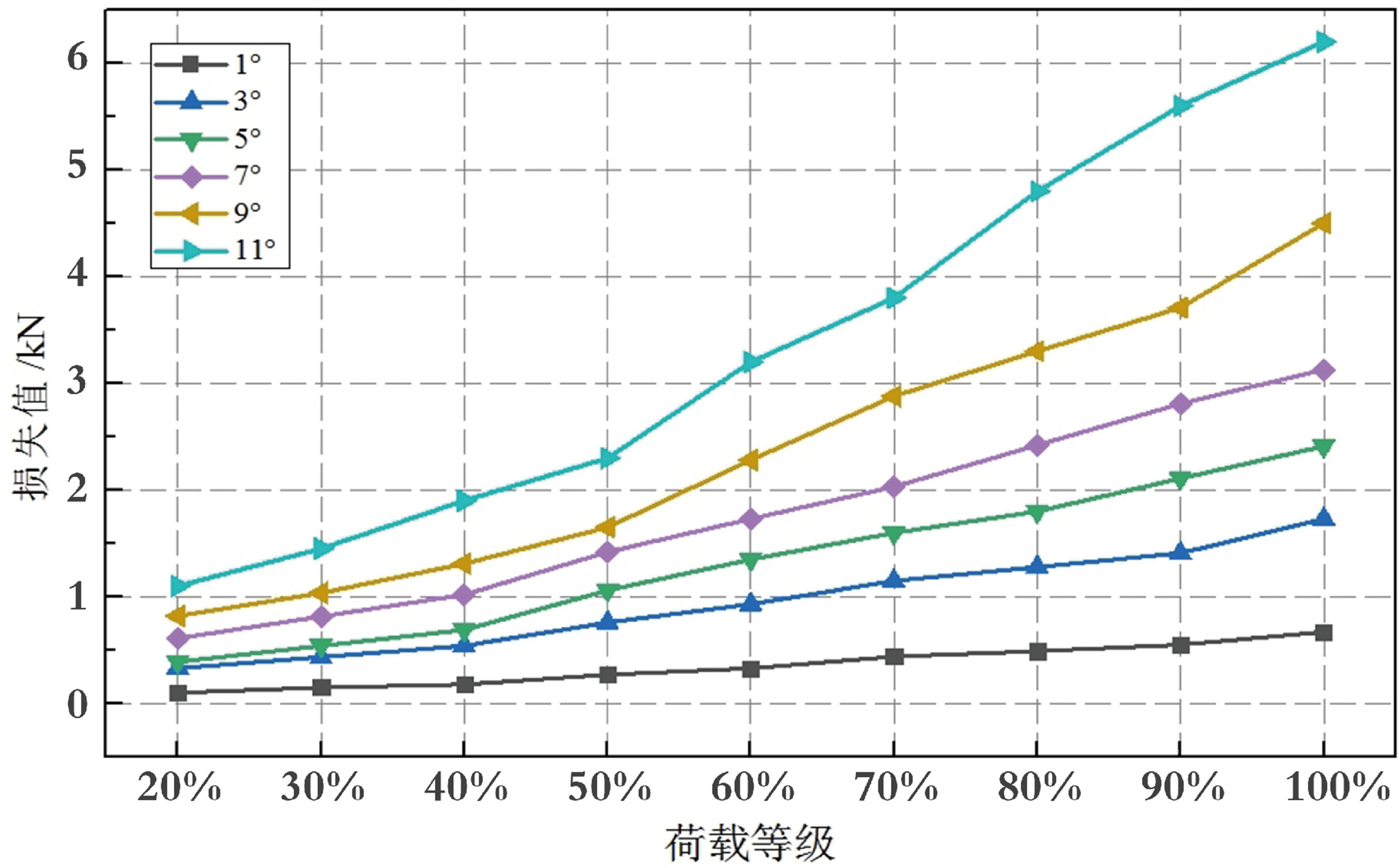
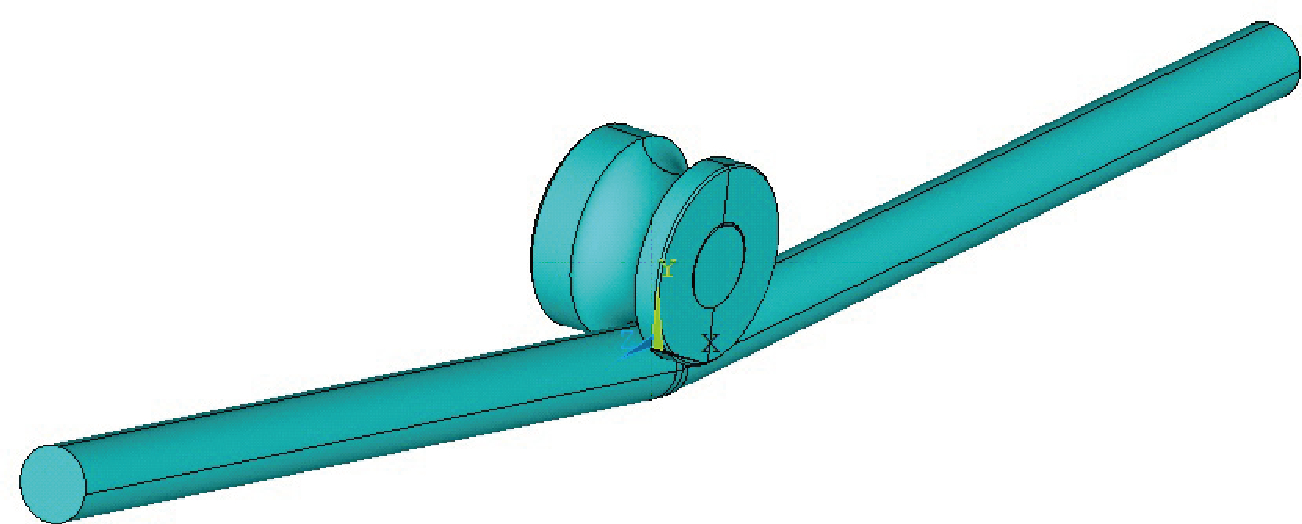



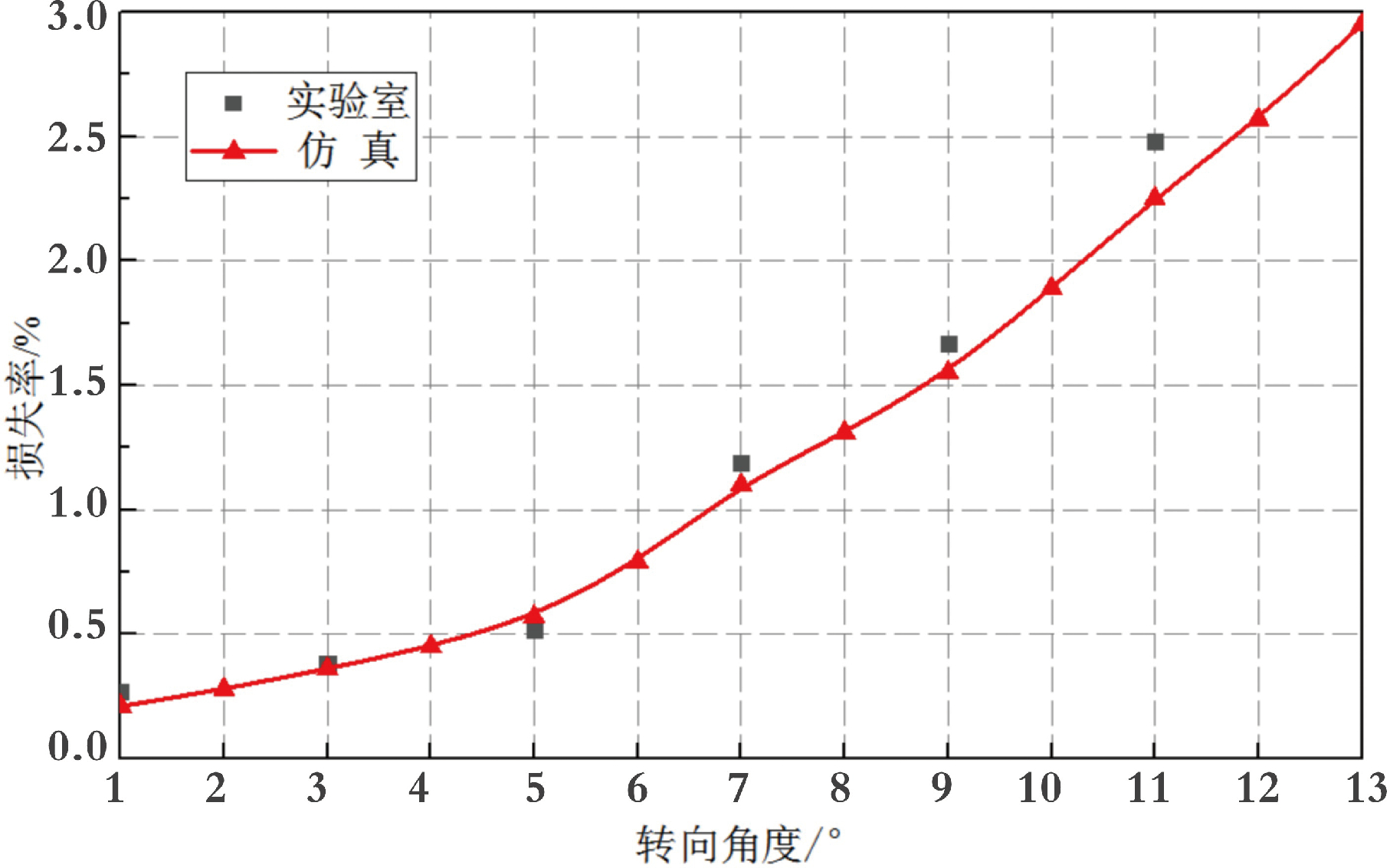


